Advanced automation/Self-maintenance and repair
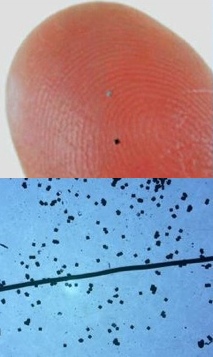
If complicated physical systems were able to be serviced and repaired completely automatically there would be many advantages. There would be higher productivity and efficiency without people in the loop - we tend to slow things down and are error prone; also people could be freed up to do something less menial; and the systems could scale quickly when more capacity is needed.
Machines today, such as industrial machinery, are designed to be looked after and serviced by people, and it would likely need artificial intelligence beyond our current capabilities to maintain or repair these systems completely autonomously. However it is feasible to design them from the outset to be maintained autonomously; designed in a modular fashion with components easily removed and replaced by another machine, and embedded wired or wireless sensors giving the ability to diagnose faults on all significant parts.
Many parameters can now be sensed with solid-state or micro sensors, manufactured on tiny silicon chips, which can be embedded within functioning machines. If the signatures from multiple sensors relating to each machine function is known when operating within normal bounds, it provides a method for pin-pointing problems with great accuracy. Vibration, temperature, rotation, pressure, distance, voltage and acceleration as examples. Operations can be assessed in real-time and if there is a failure then the defective parts, or whole assemblies can then be replaced without requiring human intervention.
The physical aspects of the machines would also have to be designed with autonomous replacement in mind, with magnetic, RFID or optical cues that can easily be read by a repair robot, and modular physical design of components allowing them to easily be extracted and replaced. For instance, a gearbox that slots in or out as a single cartridge.